填補我國技術空白,國內首套氧化鋁焙燒智能系統投運
IT之家 5 月 15 日消息,綜合科技日報報道和中鋁沈陽鋁鎂院消息,中鋁國際沈陽鋁鎂設計研究院有限公司自主研發的國內首套氧化鋁焙燒智能優化控制系統,在山西信發化工有限公司正式投運。該系統填補了我國在高溫焙燒過程智能控制領域的技術空白,將焙燒爐溫度波動控制精度提升至國際領先水平。
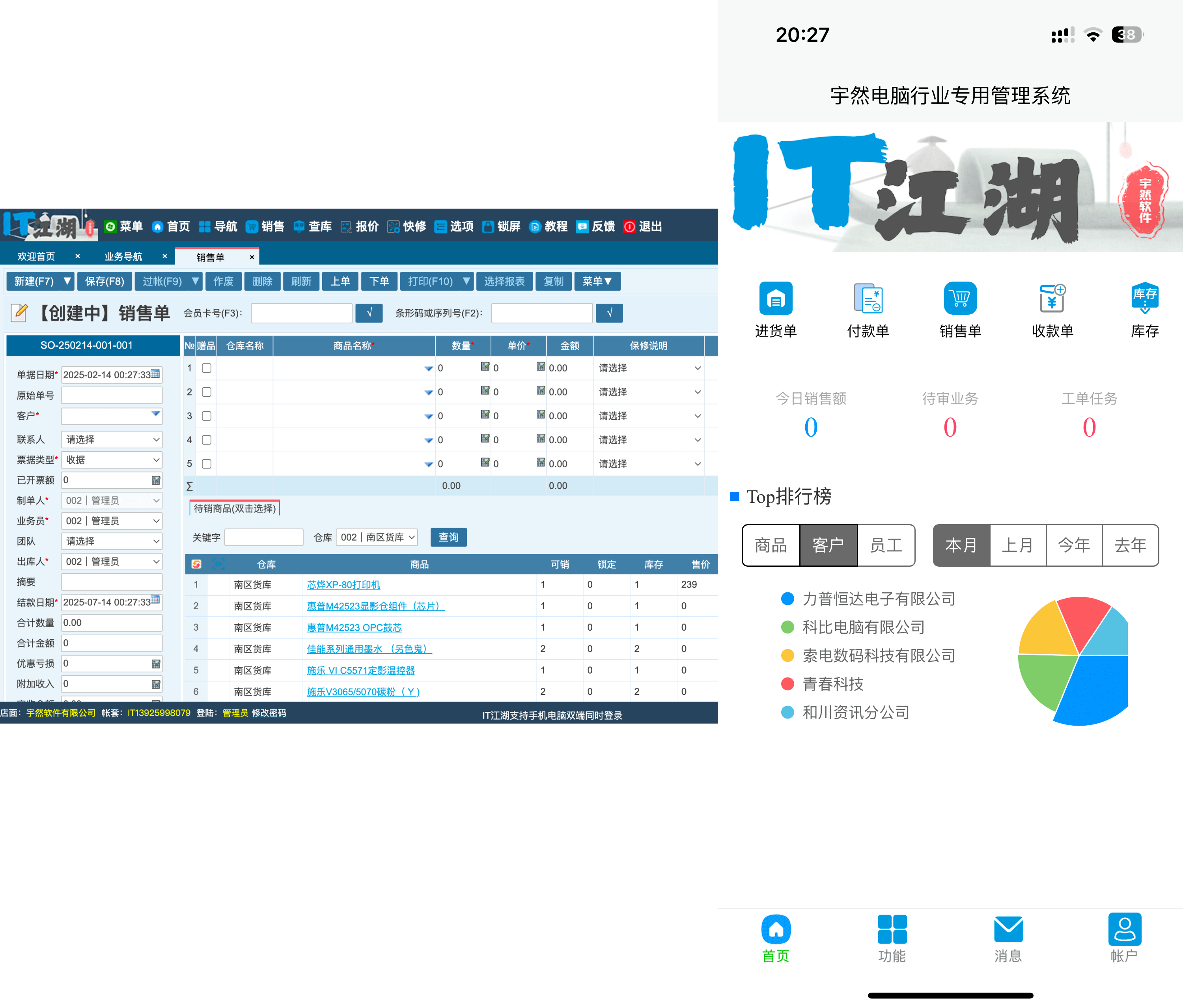
▲ 圖源中鋁沈陽鋁鎂院:山西信發化工有限公司焙燒爐項目團隊負責人梁綿鑫表示,氧化鋁焙燒工序堪稱制造業的“高溫黑箱”,其爐內持續千攝氏度高溫環境,物料停留時間、溫度場分布等關鍵參數長期依賴人工經驗調節,產品質量波動大、能耗居高不下。
氧化鋁焙燒智能優化控制系統創造性引入非平穩時間序列因果溯源分析技術,開發出國內首個強化學習控制模型,實現了焙燒生產過程自主調節,攻克了傳統控制手段難以應對工況突變的行業痛點。
IT之家查詢獲悉,該系統于去年 12 月前后正式上線并通過驗收,其采用基于動態矩陣控制 (DMC) 和自適應控制算法的先進控制策略,實時調整溫度控制參數。同時引入了智能優化策略,基于大數據分析和機器學習技術,通過歷史數據和實時監測數據建立非平穩時間序列模型 (ARIMA),以智能方式來預測和優化 PO4 溫度的最佳控制曲線。
該系統在滿負荷試運行中,成功應對燃氣壓力大幅波動的極端工況,將焙燒爐的溫度波動控制在目標值 ±2% 以內,領先于國際上 ±5% 的水平。山西信發化工有限公司生產數據顯示,該系統投用后每噸氧化鋁熱耗降低 3.2%,按企業年產 300 萬噸規模測算,年節約生產成本超千萬元。
來源:IT之家